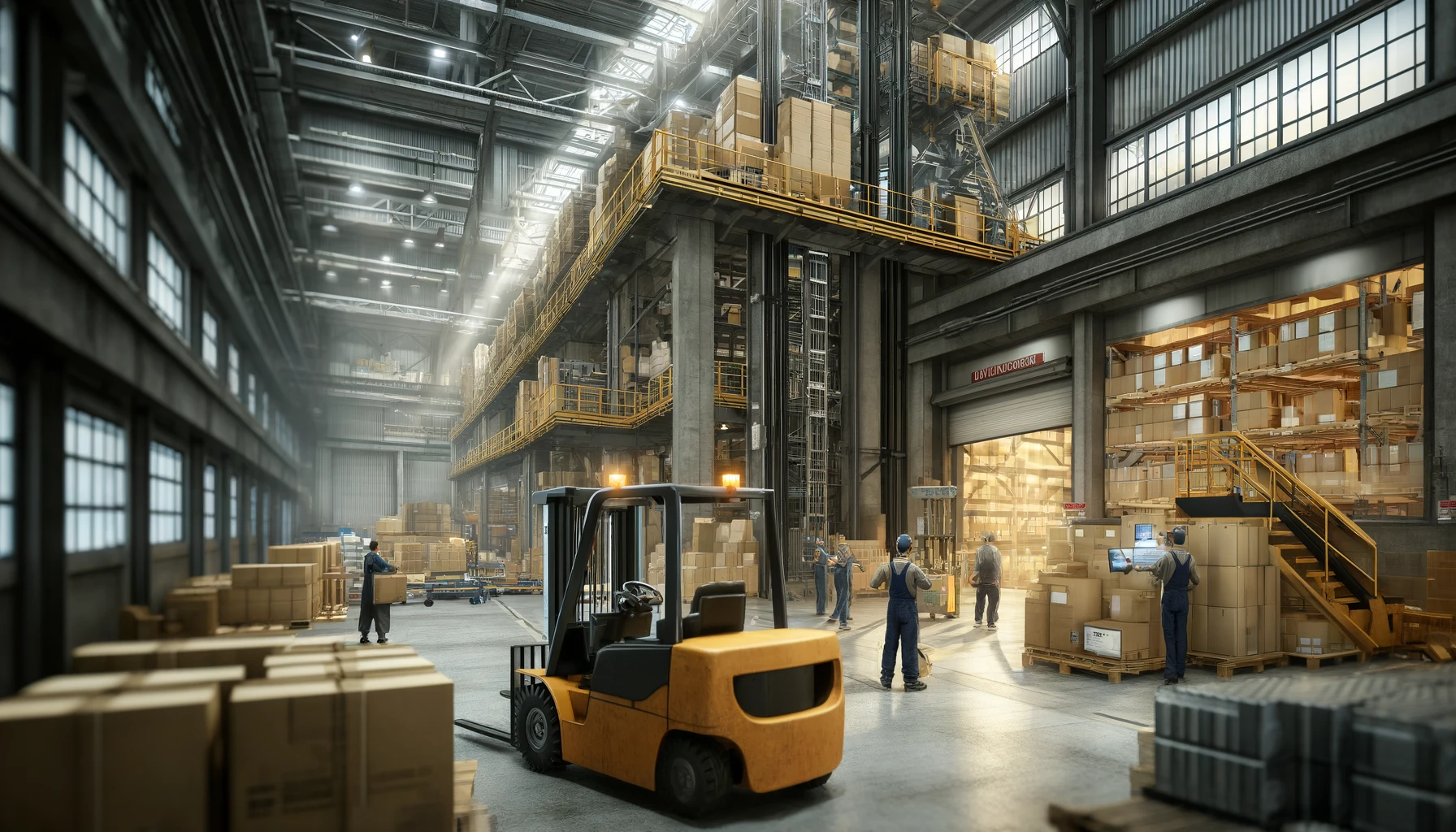
In the rapidly evolving manufacturing sector, one organization embarked on a journey to redefine their workplace safety standards. This initiative, born from a partnership with Protex AI, aimed to harness the power of computer vision to mitigate risks, prevent accidents, and foster a proactive safety culture.Â
Despite rigorous safety protocols, the organization faced ongoing challenges with high incident rates and compliance issues, highlighting the need for a more proactive approach to risk management.Traditional safety measures, while comprehensive, lacked the proactive approach necessary to address the complex safety landscape of modern manufacturing environments. High incident rates, compliance difficulties, and the absence of real-time risk assessment mechanisms underscored the urgency for a transformative solution.
Deployment of Protex AI
The Approach
Protex AI was able to be integrated seamlessly with the facility's existing CCTV infrastructure. This approach enabled continuous, automated monitoring across the facility, providing an unprecedented level of insight into everyday operations and potential safety hazards.
Key Safety Rules Implemented
To tailor the technology to the facility's specific needs, several high-impact safety rules were deployed:
- Unauthorized Area Entries: This rule aimed to detect and prevent personnel from entering hazardous or restricted areas, thus reducing the risk of accidents involving unauthorized access.
- Close Encounters Between Personnel and Vehicles: By identifying near-miss incidents between moving vehicles and pedestrians, the system could prompt immediate corrective actions, enhancing pedestrian safety in high-traffic areas.
- Compliance with High-Visibility Safety Gear: Ensuring that all personnel in critical zones wore high-visibility safety gear was crucial for preventing accidents, especially in low-light conditions or areas with operational machinery.
- Pedestrian Safety Near Operating Machinery: The system closely monitored zones where machinery operations intersected with pedestrian pathways, minimizing the risk of accidents through timely alerts and interventions.
Results and Impact
The implementation of the Protex AI system brought about significant and broad improvements in workplace safety metrics:
- Dramatic Reduction in Safety Events: In the month following the deployment of the Protex AI system, the facility experienced a notable decrease in overall safety incidents by over 60%, indicating the system's effectiveness in proactively mitigating risks.
- Enhanced Proactive Safety Reporting: The period post-implementation witnessed an exponential increase in near-miss reporting, growing by approximately 500%, reflecting a shift towards a more vigilant and preventative safety culture among employees.
- Focused Mitigation of Area-Specific Risks: Targeted interventions in areas identified as high risk achieved remarkable success, with incidents in these zones decreasing by roughly 90%. This demonstrates the AI system’s capability to focus on and address specific safety challenges, leading to improved outcomes in targeted areas.
ConclusionÂ
This case study exemplifies the successful application of AI in enhancing workplace safety, marking a milestone in the evolution of risk management within the manufacturing industry. The collaboration has not only yielded immediate safety improvements but also set the stage for ongoing advancements in safety protocols. As the facility continues to leverage AI technology, it remains a model of proactive safety and operational excellence for the broader industry.
‍